The definitive guide to PROFINET with IIoT!
PROFINET is a network that brings an extensive list of advantages aligned with our digital era. But what can you apply in your plant, and what are the real benefits of this digital network?
In an earlier article, we discussed EtherNet/IP and its benefits. Today, let's talk about PROFINET and how you can implement it in your plant. With all this information, you can decide for yourself whether EtherNet/IP or PROFINET works better for your application.
Industrial networks and protocols
Even though we still see 4-20mA/HART worldwide, more digital networks are gaining traction in the industrial space because they sync better with digitalization.
Discussions around why analog is still relevant are common, because it’s robust and straightforward, which keeps life in the field easier, right? But what about transparent connectivity between field and control?
With controllers or equipment that offer significant amounts of data, we find protocols such as Modbus RS485, OPC, and PROFIBUS DP. You can also work with FOUNDATION FIELDBUS H1, PROFIBUS PA, PROFINET, and many others.
These industrial networks connect field devices with controllers, sending diagnostics, supporting configurations and much more than pure analog can provide.
Yes, 4-20mA is still king in the field, mostly because of the gap between vendor concepts and user realities. Of course, the complexity of digital networks also postpones analog’s retirement.
But now we have IIoT and Industry 4.0, pushing more digitization in order for solutions to work correctly. Today, Ethernet-based protocols and wireless communication are increasingly present in new projects, and more are coming, so we need to be ready for them.
General concept of Ethernet
If you ever installed a router or device connected to the Internet, you probably used or saw an Ethernet cable, right? Many people think that "Ethernet" just means the type of cable used. In reality, the cable only represents the physical part of the Ethernet network.
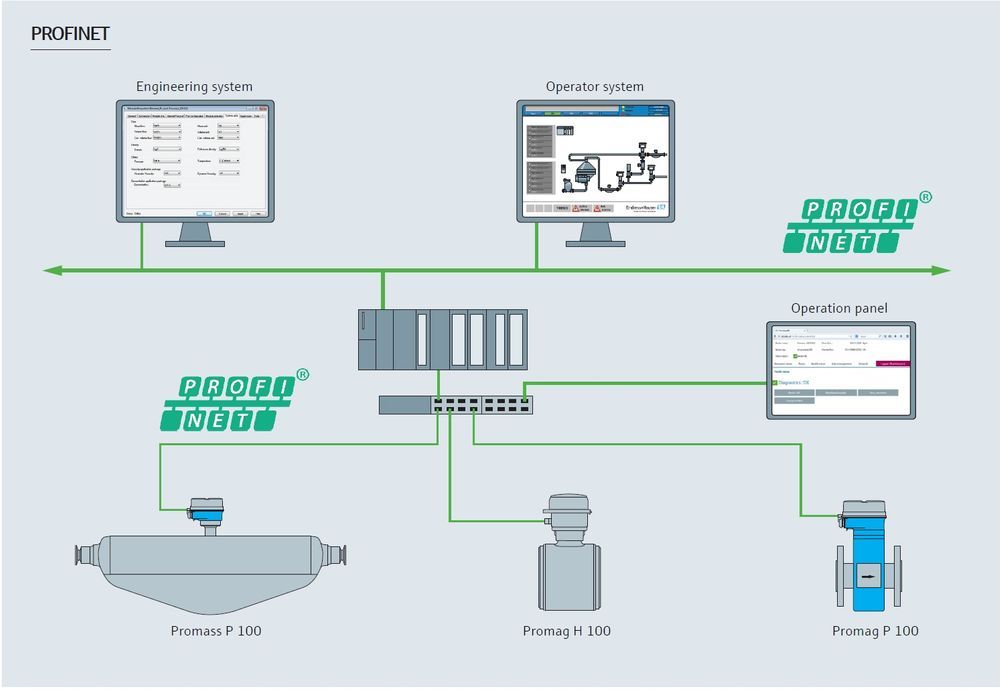
You can have many types of protocols on these cables. You’ve probably heard of at least two of them – Internet Protocol (IP) and Transmission Control Protocol (TCP). These two are the most convenient in your personal life, but in industrial use, we need more.
Industrial plants
On a plant floor, controllers must access data on drives, I/O, and workstations, and fast responses are essential. The solution also needs to withstand abrasion, humidity, and temperature changes, among other things.
So automation experts developed Industrial Ethernet. From this point, PROFINET emerged as an Ethernet-based protocol.
What is PROFINET?
This protocol connects process devices – sensors, actuators, and the like – to control systems. The PROFIBUS and PROFINET International (PI) association created it with the help of several suppliers.
It conforms to the IEEE 802 Ethernet standard in IEC 61158 and IEC 61784, meaning that you can have a printer and a flow meter on the same network! Cool, right? And PROFINET is much faster than your home network, with cycle rates in sub-milliseconds.
To explain how this works, let’s use the ISO/OSI as our reference model. For connecting two points in a network, the Open Systems Interconnection (OSI) model has seven layers. Do you know how this works?
The Ethernet standard has four simple layers:
- Ethernet for physical and data links
- IP for the network
- TCP or User Datagram Protocol (UDP) for transport
- Other protocols for the application
PROFINET usually uses these four layers, although examples such as Real-Time PROFINET can ignore the network and transport layers to accelerate response times.
Three channels exchange data with a controller in PROFINET:
- TCP/IP: Handling configurations, settings, and cyclic read/write operations
- Real-time (RT): Bypassing TCP/IP layers to speed up automation between 1 and 10 milliseconds
- Isochronous Real-Time (IRT): Switching schedules and sort signals for precise synchronization
The PROFINET I/O system
PROFINET works within the provider-consumer model of data exchange instead of the master-slave model adopted by PROFIBUS. These devices fall into three categories:
Controller
Usually, a programmable logic controller (PLC) or a distributed control system (DCS) runs the automation program. The controller sends output to some IO devices and receives input from others. It’s similar to a Class 1 master in PROFIBUS.
Devices
Sensors or actuators connected to the controller via Ethernet cables exchange data with the controller, similar to slaves in PROFIBUS.
Supervisor
PCs, human-machine interfaces (HMI), and other monitoring, commissioning, or diagnostic devices act in a similar fashion as PROFIBUS Class 2 masters.
To configure a PROFINET IO system, you need at least one controller and one device. But you can configure systems in many ways: multiple controllers for a single device, a single controller for various devices, or various controllers for multiple devices.
Typically, you use supervisors temporarily for troubleshooting and commissioning.
A PROFINET system also has network components, such as switches and wireless access points. Some components can function as IO devices for enhanced diagnostics.
Configuring PROFINET devices
To configure a PROFINET IO device, you need two things: a tool to act as supervisor and a General Station Description (GSD) file. Your vendor will supply this GSD file, and it resembles the files used in PROFIBUS. However, it’s based on XML, called GSDML here.
After configuration, the GSDML file downloads to the controller, connecting it to the devices. Inputs and outputs flow between the devices and the controller as cyclical data. Other information, such as diagnostic data, moves as acyclic data.
The difference between PROFIBUS and PROFINET
So which one should you use, PROFIBUS or PROFINET? If you’ve read my other articles, you already know my answer here, but for the new people – the best option depends on several factors in your application.
Basically, PROFIBUS is a traditional digital protocol based on serial communication. PROFINET is a new protocol based on Industrial Ethernet communication. PROFINET supports faster communication with more bandwidth, allowing larger data packets than PROFIBUS.
Here’s a spreadsheet to give you an overview of the differences between PROFIBUS and PROFINET:
Another advantage of PROFINET is that you can use it with proprietary wireless communication. PROFINET is an Ethernet standard, so you can use WIFI and Bluetooth – if they make sense in your application, of course!
PROFINET and IIoT
Connectivity and openness are the key to efficient IIoT systems. It’s important to collect field data for relevant insights, and PROFINET provides a straightforward and transparent connection between field devices and IIoT cloud-based services.
The coexistence of PROFINET with other protocols allows operators to enter the digital age using a familiar physical medium. Also, you can export data from the field to high-level systems with a cloud database using another open standard together with PROFINET, such as OPC UA.
We’ll dive into more details in the next article, but now you know PROFINET is already a part of the IIoT era. Don't forget to have a look also in Ethernet APL; we will discuss it soon.
If you learned something useful today, please share the article on your social media using the #Netilion tag.
Stay healthy, and see you next time!