Everything you need to know about the HART Communication Protocol and Industrial Internet of Things.
HART field devices give to us tons of high-level data, but there are still companies out there leaving the information in the field. How do you solve it?
We tend to believe that our companies are far removed from the innovation that pops up all of the time. There are, of course, many concerns regarding the adoption of new technologies. One that often crops up is the cost of revamping the plant to be ready for the new stuff.
On the downside, many people don’t want even to start the conversation on the possibilities of applying a new solution. On the upside, there are people like you! Yes, I am talking to you, the readers of this article.
Even if you still have some doubts about the new Industrial Internet of Things, you are open to hearing more about its benefits, and for sure, you are free to run a test depending on how straightforward and affordable the solution is, right?
Listen, I am glad you are here today! Let’s both have a look how the HART Communication Protocol still provides meaningful information, and what the possibilities are to have a low-cost integration into IIoT cloud computing with your HART devices out there in the field.
Stick around, get yourself a drink and let me tell you how to beef up your plant using HART field devices and HART interfaces - or HART gateways, as they are also known.
A day in a plant with 4-20mA/HART.
It was a rainy day, and I had a feeling I was in for a super chill out with not too many calls from the operators. Guess what? I didn’t know yet, but I was wrong. It was one of those days where everything decides to go wrong at the same time.
I used to work in the maintenance team, and most of the time I was doing daily tasks, such as calibration, cleaning devices, installing new things and taking with the operators.
Yes, I look back and see myself trying time and time again to get it into their heads that the flow meter was measuring correctly and the problem was with the process.
Sometimes, we used to get some emergency calls when a device was not working and we had to find out as quickly as possible what was going on. Usually, the maintenance team was familiar with all the bugs and a couple of issues that happened quite often.
Back to the rainy day: I didn’t want to go into the field because it was raining heavily. In addition, I had some students with me and most of the team was out doing training. Later on, I got a call from the operator about a level measurement.
I saw myself getting drenched just walking to the measuring point, but I got my tools together and trudged out into the rain. Level transmitter LT-305 just had to be as far away as possible from my workshop, of course.
On my way there, I got another message from the operators saying that they were running the process without the measuring point.
I saw it was a serious call and hurried to get there as fast as I could. When I arrived at the device, I got my first surprise - no local configuration. The operator had explained that the measurement was fluctuating and they that didn’t have the level information.
Then, to find out what was happening, I got the field configurator from my toolbox to read the device data – second surprise! The field configurator’s battery was flat and I couldn’t check why the device wasn’t working.
The only thing I could do was go back and recharge the battery a bit and then return to the instrument. I think you already know what happened, right?
The operators were running the process without an accurate level measurement and they didn’t realize the level was too high. The point level switch worked perfectly, though, shutting down the process and stopping production.
Like a great rainy day for the maintenance team!
What is the HART Communication Protocol?
Do you identify with the story above? I am sure you do. This problem can be solved quickly by collecting the device data from the field. Even if the field devices were only using 4-20mA analog signals, all of them had the HART Communication Protocol. And we didn’t use it!
The HART Protocol is not new, as we all know, but although there are tons of these devices installed in different industries all over the world, the basics are still not clear to everyone.
HART means Highway Addressable Remote Transducer and the protocol was developed the mid-1980s. Only in 1986, did the HART Communication Protocol became open - before it was a proprietary protocol.
HART is a hybrid protocol where the digital signal is superimposed on the 4-20mA analog signal. Traditional 4-20mA in fact, and older than me and probably you, but still used in an awful lot of plants out there.
For the techies among you, the HART protocol was developed using the Bell-202 standard, modulates/demodulates using Frequency Shift Keying (FSK) and works at 1200 bps. The signal has two frequencies, 1200 Hz represents “1” and 2,200Hz “0”.
The technique allows the master to communicate with the slave without any interruption to the 4-20mA signal. This is just a short explanation of the HART protocol. There’s other stuff we can talk about sometime, such as HART commands, HART multi-drop, etc., but let’s save it for a rainy day!
What is the difference between the HART Protocol and the other fieldbus protocols?
HART field devices offer a similar level of data as their digital counterparts, but whereas a digital device always communicates the data whether you are using it or not, most HART devices die in the field with the data locked inside them.
All devices with the HART Communication Protocol will give you intelligent device management (IDM), which also found in the PROFIBUS, FOUNDATION Fieldbus and other digital devices.
Multi-drop - the digital way to read all the information from HART devices is very slow and not very popular. There are, however, other possibilities to rescue all this valuable information from the field without resorting to it.
So what’s the difference between the HART and digital devices? There is none regarding the level of information you can get from your field device. All types will provide the same golden data concerning device health.
On the downside, the standard way of installing HART devices means that the control system only reads the 4-20mA signal, completely different to a network with digital field devices.
On the upside, today we have wired and wireless methods to get the data from the field and turn the resulting information into relevant insights, like using in Netilion Health.
What kind of HART interfaces I can use in my IIoT Cloud solution?
Great, I am sure you’ve already had a situation similar to the level transmitter, which I told you at the beginning of the article could be avoided.
I want to show you two possibilities to rescue the IDM data from the HART field devices without expensive investment and modification in your plant.
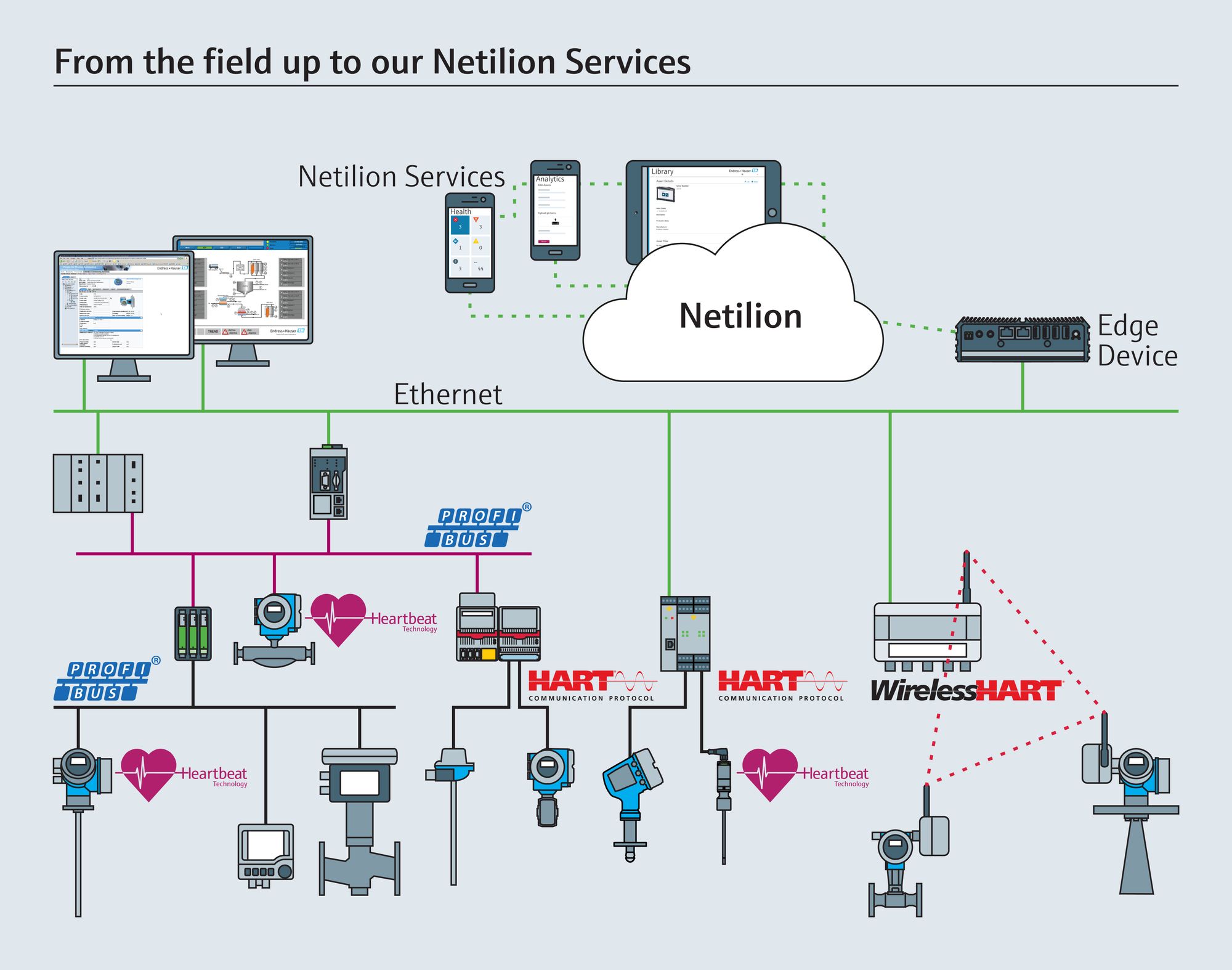
First off, I always like to say that wireless is the easiest way to collect this information. You add the WirelessHART adapter into your field devices and it transfers all the data to the WirelessHART gateway.
This WirelessHART gateway, such as the Fieldgate SWG70 from Endress+Hauser, can be integrated into the edge device and provide all the data to the IIoT cloud computing.
Wireless is already an established solution in many different industries; you can find lots of cases where end users are already using it to solve various applications. I like to say wireless is life. I mean, it sort of feels right. Can you survive without WiFi? I don’t think so.
Second off, if you still not familiar with wireless stuff, there is another great way to connect your field devices to the IIoT cloud. Yes, HART gateways are one of the straightforward ways to use the HART communication from the 4-20mA loop and integrate it into an IIoT platform, such as Netilion.
Of course, depending on the quantity and complexity, a HART gateway can represent a little bit more investment than a wireless solution. What you must keep in mind, though, is that it takes only a couple of months until the return on investment for implementing this sort of solution in your plant kicks in.
The Fieldgate SFG250, an Ethernet HART gateway, for instance is one outstanding example for implementing IIoT in your plant. HART over Ethernet is one of the simplest ways to read all the data you need without getting a headache at the end of the day!
Should I have an Industrial Internet of Things solution in my plant?
I will answer it with another question, why not? As we could see here, the Industrial Internet of Things is not as far from you as you might imagine. The benefits of IIoT services are clear; you get a lot of advantages if you implement it in your plant.
As an example, I would like to tell you how IIoT can help you to have a clear overview of your plant. Did you know that about 30% of assets in your plants are already obsolete?
Using one of the IIoT services, you can easily register your devices by hand and create a digital twin in the cloud. Alternatively, you can do it automatically by using an edge device.
Afterwards, you get access to the analytics where all the information regarding your installed base is presented transparently in powerful insights and graphs. Analytics gives you tons of information, such as an overview of all the devices and which devices are not available anymore.
This reduces the complexity and effort of maintenance effort, and much more.
The benefits of health monitoring with the HART Communication Protocol
Another powerful way of using the HART Communication Protocol and IIoT is Health monitoring. For instance, Netilion Health is one of the straightforward solutions that provides information about Endress+Hauser and 3rd party devices.
It doesn’t matter if you go wired or wireless, your HART/WirelessHART gateway can be connected to an Edge device. This will communicate securely with the cloud solution and provide all the health information no matter where you are.
In the overview page, you can see the statuses of all your devices based on NAMUR NE 107. When a device flags a diagnostic or failure, you can dig deeper into the information provided by the device and understand what the problem is and how it can be remedied.
Not only that, you also get a history of the device status and you can see when and how often the events occurred, giving you a clear picture of the situation. You never thought it could be as simple as that, right?
Now, it’s clear a similar situation to my level measurement could have been easily be avoided if the company had installed a Health system to monitor the device status. It would have saved a lot of time in solving the issue and saved a heap of money by avoiding the unscheduled downtime.
Yup, it’s as simple as that!