Why is a digital culture essential for a digital transformation?
A digital transformation in your plant needs a digital culture, not only to see the most benefits but also to avoid a culture clash that could harm your business.
If you want to start a digital transformation in your company and your team doesn’t have a digital culture, you’ll definitely encounter a lot of problems. Everyone needs the right mindset for a digital transformation, so you may need to change a few mindsets, maybe even yours!
If you think that digital culture is nothing more than work with digital software, sorry to say it but nope. It goes beyond digital tools into evolving skills, environments, and artifacts to provide relevant information and facilitate your routines.
Having someone leading a digital team lacking digital culture is like a writer who doesn’t read books. You have to get familiar and comfortable with the tools and skills to use them properly, right?
This article will show you how you can change those non-digital mindsets to create a digital culture in your company. Let’s get started!
What’s a digital transformation?
Digital transformation can mean different things, depending on your business, so it’s hard to stick with a simple definition.
We can define it for industrial automation as “the process of adding digital solutions to an application to improve operation and add value.” Sounds useful! But what does it mean? Let me give you an example.
Let’s say you have a monitoring application. You need field devices, some form of data acquisition, and a SCADA system, right? Well, if you have digital tech that supports online monitoring, then your data acquisition can happen right in your hand.
For that, you connect your field devices to an edge device that sends all your process information safely to the cloud. At the same time, you can share this information with a local solution, such as SCADA. The cloud lets you access your field-device values without setting foot in the field or control room. Sounds great, right?
While the benefits seem obvious from this overview, when this application moves from test to implementation, we often see problems with culture clash.
What’s a digital culture?
Digital culture can mean different things to different people, but we can define it here as people incorporating online technology into their work and lives. For an industrial process, the team must adopt a mindset that improves process performance using digital tools and skills.
Notice I said “team” instead of “employees.” Digital culture is collective rather than individual. Surprise! Digital tech can accelerate tasks and provide data to improve internal activities, customer support, and tool improvements, but it requires more collective thinking.
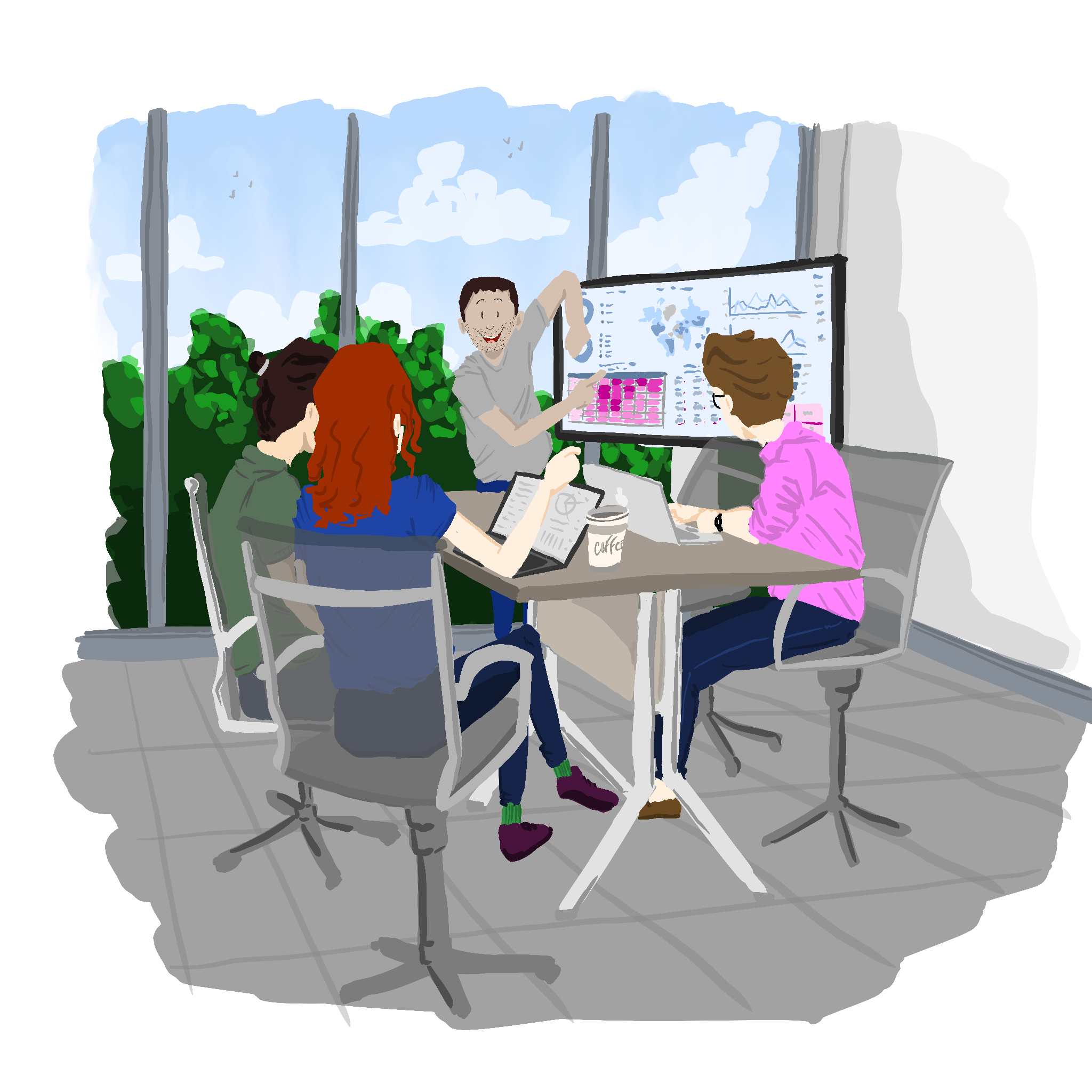
If a company lacks a proper digital culture, it may struggle to see all the potential from the technology. Based on information shared by McKinsey, these are some relevant characteristics:
- Environment with high-performing, responsible, and self-guided individuals
- Extraordinary and positively integrated teams
- High-level discipline
- Ability to move quickly
- Strong digital strategy
- High execution capacity
- Talents and digital champions
- Long-term focus
- Passion for risk
Why is a digital culture important in industrial automation?
The industrial environment tends to be very conservative toward solutions. Here, we have major concerns about switching from our tried-and-true 4-20mA to digital tech or from old maintenance procedures to new and more efficient techniques.
And of course, industrial applications need solutions that cover security and safety requirements. That’s fine, because digital technologies offer new ways to improve these points as well.
It’s easier to say “if it ain’t broke, don’t fix it” than to analyze an asset’s performance and work to improve it on an analog system. But online data and history give you more in-depth knowledge and make it clear and simple to review and improve performance.
Digital tech also provides user interfaces that make it easy to interpret data. However, monitoring still needs to be a daily task so you can understand asset behavior and learn to spot problems before they happen.
A digital culture is vital to help you make decisions and improvements in your process with digital tech. If your team doesn’t have it, you’ll lose some of the best benefits of your new tech.
A digital service to simplify your life
It may sound like a lot to do. It may even sound overwhelming, but it doesn’t have to be. You can start with a simple implementation, to gradually change both the process and the mindset.
Digital solutions are often divided into services, allowing small, easy applications to daily tasks.
The team can analyze different digital services for a routine point of a process, like monitoring. Step by step, you can get familiar with digital solutions and learn how to think differently about solving problems.
The market has many types of services, where you can improve the monitoring of your installed base, track the health of your field devices online, and more. You can choose whichever service solves your most significant pain and start to evolve to a digital culture, maximizing the technology to your benefit.
That’s it for today. If you liked this article, please share it on social media using the #Netilion tag.
See ya soon!