What are the types of industrial maintenance and how can IIoT help?
How can IIoT services fit into each type of industrial maintenance? And how do you get to predictive maintenance in your plant? See all the answers, right here!
What’s the best scenario when we talk about maintenance? I guess you will agree with me that it’s when you can avoid any problem before it happens - that sounds like an ideal scenario, right? However, many industries are not there yet, even though some of them are walking fast to reach the goal.
If we try to understand what’s going on, we can say these industries are not there yet - not because of the technology, but maybe because of the complexity of understanding the data.
In daily life, the technical team won’t have time to figure out the meaning of the data coming from the field and then plan on top of that.
What happens is, you have your daily tasks that fill most of your day, giving you no time to figure out how these complex solutions work. Today, however, Industry 4.0 and/or Industrial Internet of Things solutions are bringing a different perspective regarding such data analyses.
You don’t have to be a rocket scientist to understand the information from smart devices. The dashboard and services applied in IIoT solutions provide a straightforward way to understand what’s going on.
That makes the evolution from corrective to predictive maintenance smoother and faster than ever before. To get there, though, we could gradually implement these solutions in another type of maintenance, until the goal of the predictive reality is reached.
What kinds of maintenance are we talking about, however, and how can IIoT be implemented in each scenario?
Stick around, and let’s find out the answer to these questions together.
Industrial equipment criticality
First off, it’s relevant to understand that there is a different level of criticality for each piece of industrial equipment. Normally, devices are divided into criticality level A, B, and C.
Based on the level of criticality, the equipment or devices require increasing attention from the maintenance team in order to avoid a shutdown of the process, for example.
When we refer to equipment with criticality level A, it means it is essential to the production process and upkeep of its quality. Usually, when you have a problem with this equipment, your production line will be affected and shut down - it’s almost inevitable that this happens.
Looking at equipment with criticality level B, we are talking about equipment that may have some affect the production but will not stop it. Of course, these problems will give you a headache, but they can usually be solved, if temporarily, with the process running. That might that a proper fix of the equipment is pushed forward to a scheduled downtime.
Finally, let’s look at devices with a criticality level C. When a failure happens with this equipment/device the production will not be affected. The fault can be remedied later even if the device has failed or is running without a reasonable accuracy.
Why am I mentioning the criticality level of industrial equipment? Depending on the level of criticality, different types of maintenance will be required. For instance, when we talk about planned corrective maintenance, most probably the device failure is seen as level C.
This means, it doesn’t affect the production process in the short-term. However, equipment levels B and A can require preventive or also predictive maintenance to avoid unscheduled downtimes.
What is corrective maintenance?
Corrective maintenance is widespread daily occurrence in any industrial sector. This type of maintenance helps when a device fails during operation. Usually, there are two different types of corrective maintenance, the planned and the unplanned.
Unplanned corrective maintenance happens when a device with high-level criticality fails and you need to work on it as soon as you can to make the process run again.
When it happens, you most probably have a shutdown and you are losing money for every minute the production is stopped. In some cases, you can also lose primary material and final products.
Planned corrective maintenance happens when a device or equipment with a low level of critically fails but has no effect on production. In this case it’s possible to plan its maintenance - but even this type of maintenance may not be the best solution.
How to use IIoT during corrective maintenance?
When a device fails, it’s crucial that you get it to work again as soon as possible. In this case, IIoT services can be applied to accelerate the maintenance process.
For instance, you could use a combination of smart tablet, working as a handheld, and an IIoT service to get access to the documents concerning the equipment under maintenance.
For example, you could use the Field Xpert SMT70 or Field Xpert SMT77 together with Netilion Library. This will help you to get fast access to the device files and documentation, as well as to set up the device again using Field Xpert’s outstanding user interface.
Later, if you want to move to online monitoring, Netilion Health can be a significant upgrade to avoid this sort of situation in your plant, right?
What is preventive maintenance?
Now, it’s time for preventive maintenance. As we can see, its name is self-explanatory, right? All actions regarding preventive maintenance focus on decreasing unplanned failures by making sure the devices are kept in good working order.
Preventive maintenance can be based on a time frame. That means, for example, you have to clean a device and change some items every two months. It can also be based on device utilization, meaning after 2000 movements the oil should be replaced, for example.
Finally, you can also do preventive maintenance based on the production, meaning after 5000 products it’s necessary to do some cleaning and to change some basic stuff.
In industry, preventive maintenance is commonly applied with the focus on avoiding unplanned failures and increasing the lifetime of equipment.
How to use IIoT during preventive maintenance?
Here, you can also use your industrial tablet, such as the Field Xpert together with IIoT services. First off, it’s essential to have a big picture of your plant and the devices and equipment installed there. This helps you to plan which items have to be replaced during preventive maintenance.
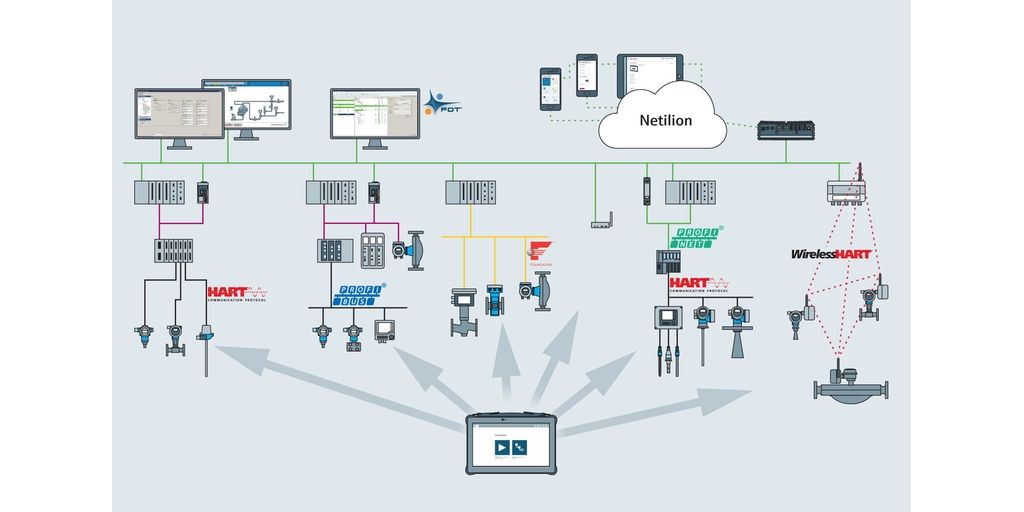
Here, Netilion Analytics is a great option to provide a clear view of your plant and help you to plan your preventive maintenance. On top of that, Netilion Health can offer the history of health conditions of each of the devices connected to the solution.
It will help you to understand what is going on with these devices.
What is predictive maintenance?
Everyone wants to be at this level, but so far, it was not very simple to reach it. Predictive maintenance is done when you have online or frequent monitoring of your devices to check their health and see if it changes.
Based on this data from the devices, it’s possible to know if any action should be done before a problem happens – Yup, you sort of see into the future! Usually, when we talk about big machinery, you have constant monitoring by measuring different points and, based on spectrum ODS (Operating Deflection Shape) and other techniques, it’s possible to see if any action is required.
On the process automation side, it’s essential to collect the data from the smart devices and understand this information. The new IIoT services provide a comfortable and intelligent way to understand the data coming from your smart devices in the field.
On the downside, one of the significant challenges here is how to collect this information because the majority of the devices out there still have only analog 4-20 mA signals – a sad reality!
On the upside, there are new possibilities that make accessing this information simpler than ever before. For instance, WirelessHART and Bluetooth devices are a simple way to get this data integrated into field edge devices and then into a cloud solution.
How to use IIoT during predictive maintenance?
IIoT services are essential to have predictive maintenance running smoothly. However, before taking any action it’s crucial to check the information you want yourself and then base all the planning on the data provided from the IIoT service.
What’s different than before is that new IIoT service solutions, such as Netilion, provide a straightforward away to understand the information.
You don’t have to be a data analyst to see what’s going on!
This is one of the biggest benefits of IIoT services: the simplification and interpretation of the data collected from the field.
How to implement the concept of predictive maintenance in your plant?
The first step is to change the mindset of the team from a reactivate to a proactive approach.
For that, it’s essential to collect information from the devices in the field. Today, it’s super simple to collect this data without high investment or changing all the instruments in your plant.
Below, I’ve listed some articles with more information regarding this topic:
- Everything you need to know about the HART and Industrial Internet of Things
- How to take the first steps towards IIoT using WirelessHART
- A simple way of adding IIoT to a PROFIBUS network
- How to connect your Bluetooth instrumentation into the IIoT Cloud in 3 simple steps
After that, you need to integrate this information into the cloud. Here, the field edge device is essential to provide the integration into the cloud.
You can read the articles below to understand the possibilities regarding them:
- What is an edge device, and why is it so crucial to IIoT?
- What do you need to know about digital twins?
- 7 questions to find out if you can implement the Industrial Internet of Things
- Cybersecurity in industry plants with IIoT: What really counts.. and how safe is Netilion?
Finally, you have to sign-up to an IIoT service, such as Netilion Health, Library, Analytics, or Connect. These services bring unique features to make your plant smarter than ever.
I took the freedom to list these options for you, see the links down below:
After all these steps, you’re going to have access to all the data no matter where you are and what kind of device you like most: smartphone, laptop, tablet, etc.
As I said before, more and more companies are moving quickly to reach the predictive maintenance level and use the digital data to increase productivity, reduce downtimes and ensure the quality of production.
How about you?
If you liked this article, don’t forget to share it on your social media using the #netilion
See ya!